Kistler is your competent partner for sophisticated measuring applications in the field of R&D – e.g. for vehicle testing and aerospace testing; for monitoring processes in industrial manufacturing; for condition monitoring of sensitive infrastructure in the public sector; for protecting roads, rail and road users. Digital solutions include software applications that help you manage big test data.
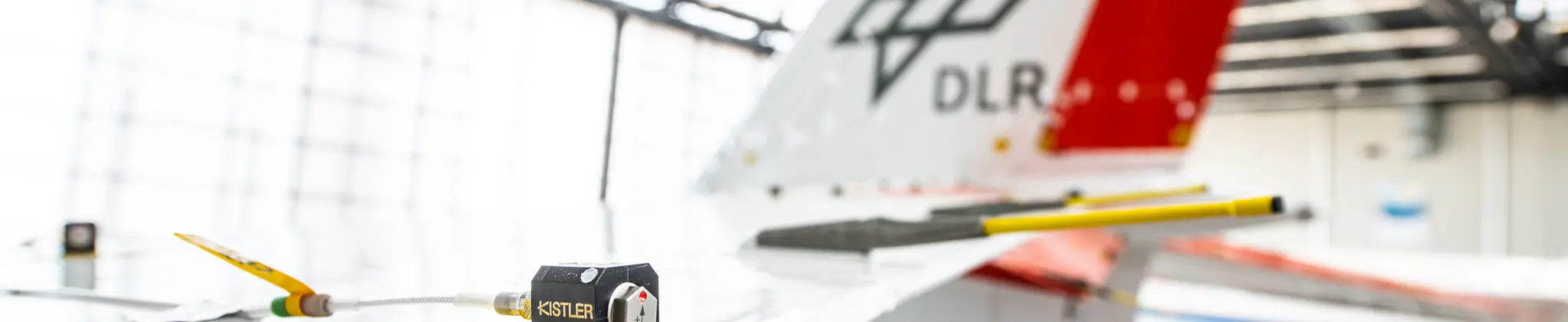
Applications
Innovative measuring technology for industrial applications and monitoring of public infrastructureIndustrial solutions
Advanced manufacturing
Research and development solutions
Automotive
Maritime
Biomechanics and sports
Traffic and infrastructure solutions
Need a consultation?
Our experts are just a click away.