There’s no doubt that the future of electromobility depends on two factors: expanding the ranges that vehicles can achieve, and continuing to develop charging infrastructures. But how would it be if all vehicle users could charge their vehicles safely and flexibly themselves? No matter where, no matter when – with smart monitoring and billing functions included? Juice is a Swiss company that has taken this vision as its mission. Their charger plug solutions can replace the classic ‘wallbox’ home outlet in terms of power – yet they also remain mobile and flexible: depending on the facilities available, they ensure a secure, efficient and controllable charging process with up to 22 kW.
BGF EnzTech relies on quality assurance by Kistler in its punching process for charger plugs
BGF EnzTech has quickly made a name for itself in the electromobility, power feed and temperature monitoring sectors thanks to its precision-manufactured hybrid components and assemblies. Quality assurance by Kistler plays a key part in the production of charger plugs with integrated temperature monitoring. Kistler technology guarantees high quality in the punching process, as well as ensuring protection for valuable machines and tools.
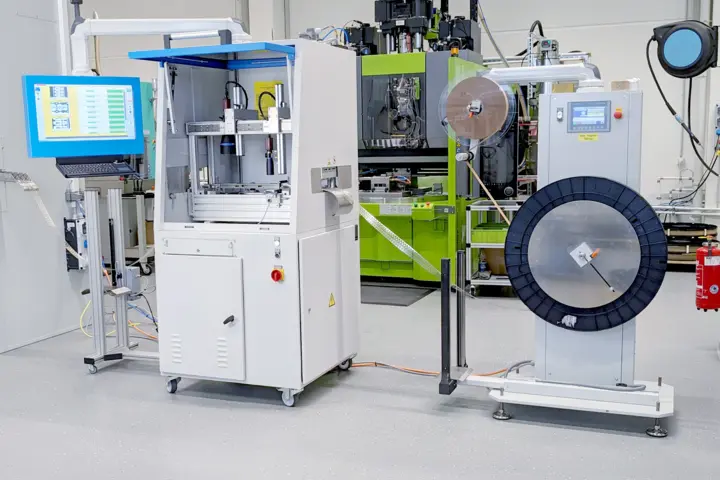
Value chain for innovative charger plugs built up in just a few years
Most of the technology behind the enterprise originates from a young company named BGF EnzTech, which was established in 2016 at Pforzheim (Germany). “People used to ridicule us back when we founded the company – which was still called E-D-A GmbH in those days. The letters stand for three German words that mean development, design, and automation. Hardly anyone took us seriously,” says Julian Bucher, who took over as CEO of this family firm in 2023.
“Since then, we’ve been very successful with our power feed and temperature monitoring products – even beyond the electric car sector.” Following a development phase of around two years between 2016 and 2018, the company set up a complete production line for Juice. This means BGF EnzTech can now cover the entire value chain for the charger plugs with integrated temperature monitoring, from the original idea through to production – with a high level of vertical integration, including toolmaking and other manufacturing equipment. Customers in segments such as electric motor production (for fans, pumps, escalators and more) and also in the aerospace industry appreciate this know-how and the company’s high standard of quality: BGF EnzTech customers receive complete modules consisting of complex hybrid components, including seals, assembly and finishing – all from one single source.
Partnering with Kistler to meet high quality standards in the punching process for charger plugs
When it comes to temperature monitoring for the Juice charger plugs, BGF EnzTech now offers twelve variants of its T2X (Temperature-to-X) product for different countries and power systems. Temperature monitoring ensures that the charging process for electric cars is safe, reliable and optimized: if the charger plug becomes too hot, the electronics reduce the charging current in several steps and, if necessary, switch off completely.
After its success in Germany, BGF EnzTech gradually went on to conquer the markets in Italy, Switzerland and the UK, followed by the USA – where conditions are highly dynamic at present, although the power system operated there is entirely different compared to those used in Europe. Bucher continues: “This meant that the outlay was far higher, not only because of the four plug variants that are customary there: we also had to obtain the UL (Underwriters Laboratories) certification that’s essential for the US market – for the products themselves, as well as for our entire production.” Today, BGF EnzTech is one of only three companies in Germany that meet UL standard 817.
Over the course of just six months, the company set up a dedicated punching line (in addition to the total of four injection molding lines) – equipped with Kistler measurement technology from the outset. “Given our quality standards and the complex nature of our products, it was clear that we weren’t going to leave anything to chance here. Kistler is a name that stands for quality, and their geographical proximity to us also made our decision easy,” Bucher recalls. In the punching machine, special light barriers and analog inductive sensors from Kistler (such as the PMI-10-10/P/AS10-U-4, PXI-5-5/3-P and ISS-20-30-1-A) ensure that the strip is processed reliably and the tool is not damaged. Functions implemented include double sheet control and feed control, as well as strip lubrication by an oiling system. All sensor functions can be conveniently monitored via the integrated process monitoring system with 24 digital and 12 analog channels; modular expansion via the software is also possible if required.
Reliable punching processes – plus optical part inspection
“Given the varied range of parts we have and the constant flow of new projects, the flexibility of the systems we use is important to us,” Bucher continues. “Thanks to Kistler’s training courses, the possibility of remote access and – above all – their close geographical proximity, changeovers are possible at any time.” This also applies to the vision systems that check the finished punched parts or components for quality features. The KVC 621 optical inspection system from Kistler was equipped with two camera systems for BGF EnzTech: each of them checks all the dimensions and performs another special inspection of the component’s front area. Two more modules are already planned for integration into the test cell: an additional camera that measures the height of the components from the side, and a laser marking module that automatically marks identified NOK parts so they do not even enter the downstream injection molding process.
Thanks to dual quality assurance in the punching process with mutually complementary Kistler technologies – sensors integrated in the machine or punching tool, plus downstream optical part inspection – BGF EnzTech enjoys a whole range of benefits: high product quality with very high process reliability, plus long-term protection of its costly tools and machines – with rates of up to 400 punched parts per minute. Going forward, a second laser marking cell from Kistler is planned to mark the finished hybrid parts after injection molding (where process monitoring from Kistler is already in operation). This will ensure 100 percent traceability.
Safe charging for electric cars – whenever, wherever and however you want
Following their relocation, BGF EnzTech’s agenda also includes developing new markets. Final words from Julian Bucher: “As well as Australia, we’re eying the Asian region for the charger plugs with integrated temperature monitoring. We’re mainly interested in projects with high quality standards and a certain degree of complexity, where we can bring our know-how and high-quality production into play.”