The engines of electric vehicles and aircraft turbines usually run at 25,000 rpm – a significantly higher speed than conventional drives. Powertrain test stands support engineers in achieving optimum efficiency. The new precision torque flange for powertrain test stands – consisting of rotor and stator – enables them to measure exact torques at 25,000 revolutions. At room temperature, the measuring system can even handle up to 30,000 rpm, providing a reserve for load tests.
Kistler presents an optimized precision torque measuring flange for test stands
Winterthur, May 2025 – The new KiTorq 4552A precision torque measuring flange for powertrain test stands provides precise data at even higher speeds: the new system from Kistler reliably measures torque, speed and rotation angle even at up to 30,000 rpm and is, among others, optimally suited for testing and development applications in e-mobility and aviation. A larger air gap between the rotor and stator ensures an easy setup.
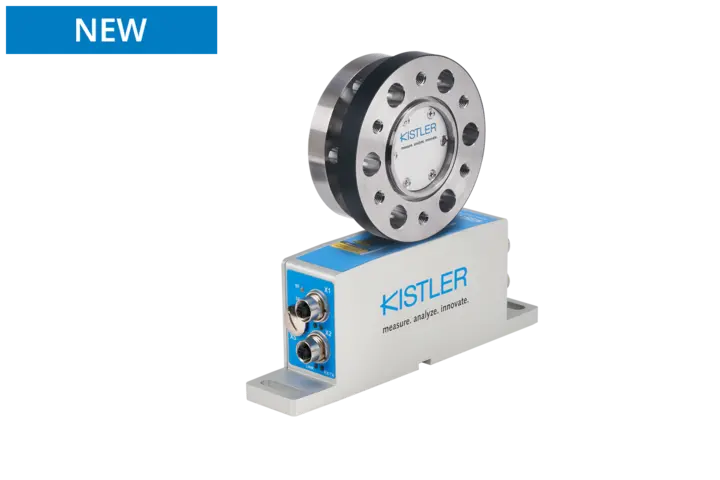
Larger rotor-stator gap simplifies setup on powertrain test stands
Kistler has increased the distance between the rotor and stator from one millimeter to nominal two millimeters to allow for an easier measurement setup. The maximum possible gap with angle of rotation and speed measurement is three millimeters – twice the maximum gap of the previous system. If the angle of rotation and speed are not being measured, a gap of five millimeters is possible. An installation aid is included as a standard feature and further supports users during the setup.
Flexible switching between multiple measuring ranges
Like its predecessor, the stator is compatible with up to five different rotors without further calibration. This reduces the amount of hardware users must handle and allows for easier switching between different measuring ranges. Once connected, the stator and rotor automatically exchange their parameters in less than a minute. As soon as the signal light on the torque flange sensor turns green, the system is adjusted and ready for use. Users can also calibrate the sensor for two torque measuring ranges to ensure more precise measurements and to avoid costs for additional adaptations and equipment. The system also enables users to flexibly switch measuring ranges with a single output or select two parallel outputs simultaneously. A free software ensures that measuring pulse interval and filter settings can be easily adjusted.
The angle and speed system is fully integrated in the sensor. With an accuracy of 0.01 degrees, the KiTorq 4552A is even more precise than its predecessor. It is flexibly adjustable, providing 1 to 8192 output pulses per revolution. Additionally, the torque output can be filtered between 0.1 Hz and 10 kHz, enabling the system to adapt optimally to various applications. Kistler stators are currently the only solution on the market that feature an integrated digital field bus or Ethernet interface in addition to an analog output. This eliminates the need for additional hardware and its calibration during setup, which otherwise would be necessary to digitalize the signal. The sensor has no bearings and is therefore completely maintenance-free – so users can focus entirely on their torque measurements at the powertrain test stand.