Die Zukunft der Elektromobilität hängt ohne Zweifel vom Ausbau der Reichweiten und Ladeinfrastrukturen ab. Wie aber wäre es, wenn jeder Fahrzeugnutzer selbst für sicheres und flexibles Laden sorgen könnte? Ganz gleich an welchem Ort und zu welcher Zeit, inklusive intelligenten Überwachungs- und Abrechnungsfunktionen? Dieser Idee hat sich das Schweizer Unternehmen Juice verschrieben: Ihre Lösungen im Bereich Ladestecker können den klassischen Hausanschluss (Wallbox) leistungsmäßig ersetzen, bleiben dabei jedoch mobil und flexibel und sorgen je nach vorhandenen Möglichkeiten für einen abgesicherten, effizienten und regelbaren Ladevorgang mit bis zu 22 kW.
BGF EnzTech setzt beim Stanzen für Ladestecker auf Qualitätssicherung von Kistler
Mit filigran gefertigten Hybridbauteilen und Baugruppen hat sich BGF EnzTech in kurzer Zeit einen Namen in den Bereichen Elektromobilität, Stromführung und Temperaturüberwachung gemacht. Eine wichtige Rolle in der Fertigung von Ladesteckern mit integrierter Temperaturüberwachung spielt Qualitätssicherung von Kistler: Sie sorgt bereits beim Stanzen für hohe Qualität und schützt die wertvollen Maschinen und Werkzeuge.
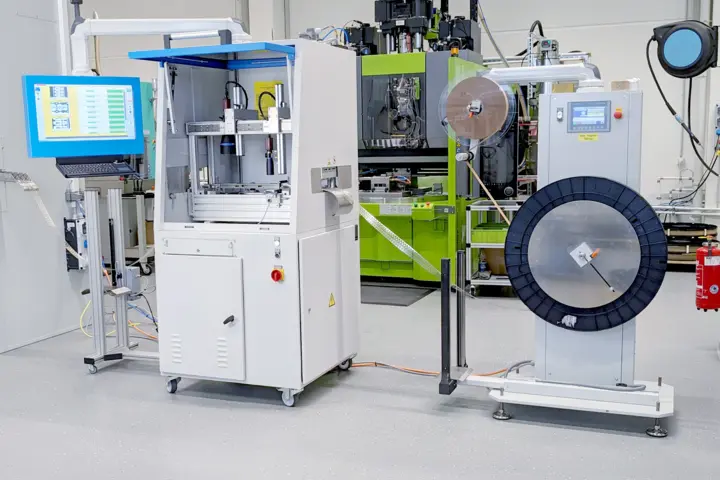
Wertschöpfungskette für innovative Ladestecker in wenigen Jahren aufgebaut
Die Technologie dahinter stammt zu großen Teilen vom jungen, erst 2016 gegründeten Unternehmen BGF EnzTech in Pforzheim (Deutschland). „Als wir die Firma gegründet haben – damals hieß sie noch E-D-A GmbH, Entwicklung, Design, Automatisierung –, wurden wir noch belächelt, so gut wie niemand hat uns ernstgenommen“, sagt Julian Bucher, der 2023 die Geschäftsführung des Familienunternehmens übernommen hat. „Inzwischen sind wir mit unseren Produkten im Bereich Stromführung und Temperaturüberwachung sehr erfolgreich, auch über Elektroautos hinaus.“ BGF EnzTech – benannt nach den Gründern Bucher, Gengenbach, Freudenberg – beschäftigt aktuell 18 Mitarbeitende, Tendenz steigend; der Umzug an einen neuen, größeren Standort (ebenfalls in Pforzheim) steht bevor.
Nach etwa zwei Jahren Entwicklungszeit von 2016 bis 2018 hat das Unternehmen mittlerweile eine komplette Produktion für Juice aufgebaut, so dass man die gesamte Wertschöpfungskette für die Ladestecker mit integrierter Temperaturüberwachung von der Idee bis zur Fertigung abdecken kann – mit hoher Fertigungstiefe inklusive Werkzeugbau und weiteren Fertigungsmitteln. Auch Kunden aus Feldern wie Elektromotorenbau (z. B. für Lüfter, Pumpen oder Fahrtreppen) und Luft- und Raumfahrt schätzen dieses Know-how und den hohen Qualitätsanspruch: Bei BGF EnzTech bekommen sie komplexe Hybridbauteile sowie ganze Baugruppen inklusive Dichtung, Montage und Konfektionierung – alles aus einer Hand.
Gemeinsam mit Kistler hohe Qualitätsansprüche beim Stanzen für Ladestecker realisieren
Im Bereich der Temperaturüberwachung für die Ladestecker von Juice bietet BGF EnzTech inzwischen zwölf Produktvarianten seines T2X (Temperature-to-X) für verschiedene Länder und Stromsysteme an. Die Temperaturüberwachung sorgt für einen sicheren und optimierten Ladevorgang bei Elektroautos: Wird der Ladestecker zu heiß, regelt die Elektronik in mehreren Schritten den Ladestrom herunter und schaltet notfalls ganz ab.
Nach Deutschland wurden schrittweise die Märkte Italien, Schweiz und UK erobert, gefolgt von den USA – dort herrscht aktuell eine hohe Dynamik, jedoch wird ein im Vergleich zu Europa ganz anderes Stromsystem genutzt. Bucher weiter: „Der Aufwand war deshalb viel höher, nicht nur aufgrund der dort üblichen vier Steckervarianten: Wir mussten nicht nur für die Produkte selbst, sondern auch für unsere gesamte Fertigung die für den US-Markt unerlässliche UL-Zulassung erreichen.“ Heute ist BGF EnzTech nur eines von drei Unternehmen in Deutschland, die die Norm 817 der unabhängigen US-Organisation Underwriters Laboratories (UL) erfüllen.
Im Zuge dessen wurde innerhalb von nur sechs Monaten eine eigene Stanzlinie eingerichtet (neben inzwischen vier Spritzgießlinien), die von Anfang an mit Messtechnik von Kistler ausgestattet wurde. „Aufgrund unseres Qualitätsanspruchs und der komplexen Natur unserer Produkte war klar, dass wir hier nichts dem Zufall überlassen würden. Der Name Kistler steht für Qualität und auch aufgrund der räumlichen Nähe fiel uns die Entscheidung nicht schwer“, berichtet Bucher. In der Stanzmaschine sorgen spezielle Lichtschranken und analoge Induktivsensoren (z.B. PMI-10-10/P/AS10-U-4, PXI-5-5/3-P und ISS-20-30-1-A) von Kistler dafür, dass das Band prozesssicher verarbeitet und das Werkzeug nicht beschädigt wird. Zu den realisierten Funktionen gehören Doppelblechkontrolle und Vorschubkontrolle sowie zusätzlich die Bandschmierung über ein Beölungssystem. Alle Sensorfunktionen können über die integrierte Prozessüberwachung mit 24 digitalen und 12 analogen Kanälen komfortabel überwacht und bei Bedarf modular über die Software erweitert werden.
Prozesssicheres Stanzen plus optische Teileprüfung
„Aufgrund unserer Teilevielfalt und immer wieder neuer Projekte ist die Flexibilität der eingesetzten Systeme wichtig für uns“, so Bucher weiter. „Dank der Schulungen von Kistler, der Möglichkeit des Fernzugriffs sowie vor allem der räumlichen Nähe sind Umrüstungen jederzeit möglich.“ Das gilt auch für die Vision-Systeme, die die fertigen Stanzteile beziehungsweise Komponenten auf Qualitätsmerkmale prüfen. Das optische Prüfsystem KVC 621 von Kistler wurde für BGF EnzTech mit zwei Kamerasystemen ausgestattet, die jeweils die gesamten Dimensionen prüfen sowie noch einmal speziell den vorderen Bereich des Bauteils. Bereits geplant sind zwei weitere Module zur Integration in die Prüfzelle: eine weitere Kamera, die die Höhe der Bauteile von der Seite vermisst, sowie ein Lasermarkiermodul, dass identifizierte Schlechtteile automatisch markiert, so dass sie gar nicht erst in den nachfolgenden Spritzgießprozess eingehen.
Dank der doppelten Qualitätssicherung im Stanzprozess aus sich ergänzenden Technologien von Kistler – in die Maschine beziehungsweise das Stanzwerkzeug integrierte Sensorik plus nachgeschaltete optische Teileprüfung – erreicht BGF EnzTech eine hohe Produktqualität mit sehr hoher Prozesssicherheit und anhaltendem Schutz der teuren Werkzeuge und Maschinen – und das bei bis zu 400 gestanzten Teilen pro Minute. Für die Zukunft ist eine zweite Lasermarkierzelle von Kistler geplant, die die fertigen Hybridteile nach dem Spritzgießen beschriftet – auch dort ist bereits Prozessüberwachung von Kistler im Einsatz –, um 100 Prozent Rückverfolgbarkeit zu gewährleisten.
Elektroautos sicher laden – wann, wo und wie man will
Nach dem Umzug steht auch die Erschließung neuer Märkte auf dem Programm. Julian Bucher erklärt abschließend: „Für die Ladestecker mit integrierter Temperaturüberwachung haben wir neben Australien auch den asiatischen Raum im Blick. Interessant für uns sind hauptsächlich Projekte mit einem hohen Qualitätsanspruch und einer gewissen Komplexität, bei denen wir unser Know-how und unsere hochwertige Fertigung zur Geltung bringen können.“